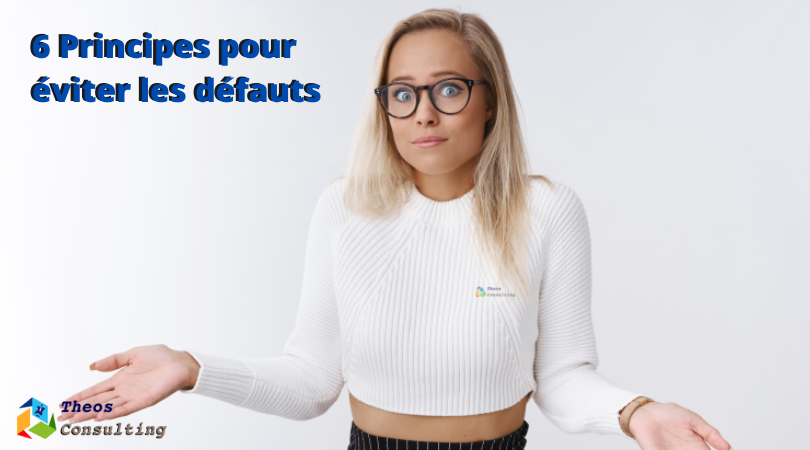
Même si le fait d’éradiquer les défauts reste un horizon, il n’empêche que c’est le but à atteindre.
De nombreux outils dans la philosophie du Lean existent, en voici une revue qui devrait vous aidez à réduire les défauts.
Le poka yoke
Très connus, mais on ne le retrouve que trop peu dans nos organisations. Son objectif est de rendre impossible, une action, une opération de la sorte que le défaut soit tout bonnement irréalisable. On peut citer de nombreux exemples autour de nous, brancher une prise à l’envers, une clé dans sa serrure, … .
Les trois principes de préventions des défauts sont :
- Réduire le risque de défauts ou de fautes.
- Réduire au minimum l’effort nécessaire à l’exécution des activités.
- Détecter les défauts avant qu’ils n’aient un impact important, certains diront à la source.
L’élimination
L’élimination vise à supprimer une étape du processus sujette aux défauts en repensant le produit ou le processus de sorte que la tâche ne soit plus nécessaire. Il peut être nécessaire de revoir la conception, de permuter des étapes d’un nouveau processus, de simplifier le produit ou de consolider les pièces afin d’éviter un défaut de pièce.
La prévention
La prévention modifie le produit ou le processus de manière à ce qu’il soit impossible de faire un défaut ou qu’un défaut devienne visible. Ce sont des moyens d’alertes physiques, visuels ou immatériels. Mais la prévention passe aussi par la formation, la formation des collaborateurs.
Le remplacement
La substitution remplace un processus par un processus plus fiable pour améliorer la reproductibilité et la répétabilité. Cela peut inclure l’utilisation de moyens liés à l’industrie 4.0 tels que la robotique, la cobotique ou autres nouveautés technologiques
Le management visuel
La facilitation est le principe le plus utilisé. Elle fait appel à des techniques et à la combinaison d’étapes pour rendre une étape du processus plus facile à réaliser ou moins sujette aux défauts. Cela inclut des contrôles visuels, notamment le codage couleur, le marquage ou l’étiquetage des pièces pour faciliter un assemblage correct ; des listes de contrôle qui énumèrent toutes les tâches à effectuer ; Une asymétrie exagérée pour faciliter l’orientation correcte des pièces.
La détection
La détection consiste à identifier un défaut avant la poursuite du traitement afin que le collaborateur puisse rapidement être alerté et corriger au plus vite. Il s’agit notamment de capteurs dans le processus de production pour identifier les pièces mals assemblées, d’auto-contrôle, de balances pour mesurer et contrôler des produits.
L’atténuation ou la limitation
L’atténuation cherche à minimiser les effets ou le défaut, lui-même. Cela comprend des mécanismes qui réduisent l’impact d’un défaut ou d’une variabilité ; des produits conçus avec des procédures de reprise simples et peu coûteuses lorsqu’un défaut est découvert. Une maîtrise du coût de reprise est nécessaire. Il n’est pas rare de trouver des zones de retouches en fin ou en cours de process dans de nombreuses entreprises.
L’éradication des défauts humaines est cruciale pour toute entreprise. Les défauts coûtent cher et ont un impact sur la satisfaction des clients. En introduisant des mesures simples pour attraper et réduire les risques de défauts, les organisations peuvent non seulement économiser des coûts, mais aussi devenir plus performante.
On retiendra :
- Le défaut fera toujours partie de nos organisations.
- La traquer, la réduire et la maîtriser doit rester un objectif quotidien.
- Le défaut nous apprends, beaucoup sur nos failles et reste une formidable source d’amélioration.
Traquons les défauts, tordons-leur le cou pour s’améliorer au quotidien.
J.Keire
theos.fr
Pour aller plus loin :
Poka yoke Citroën